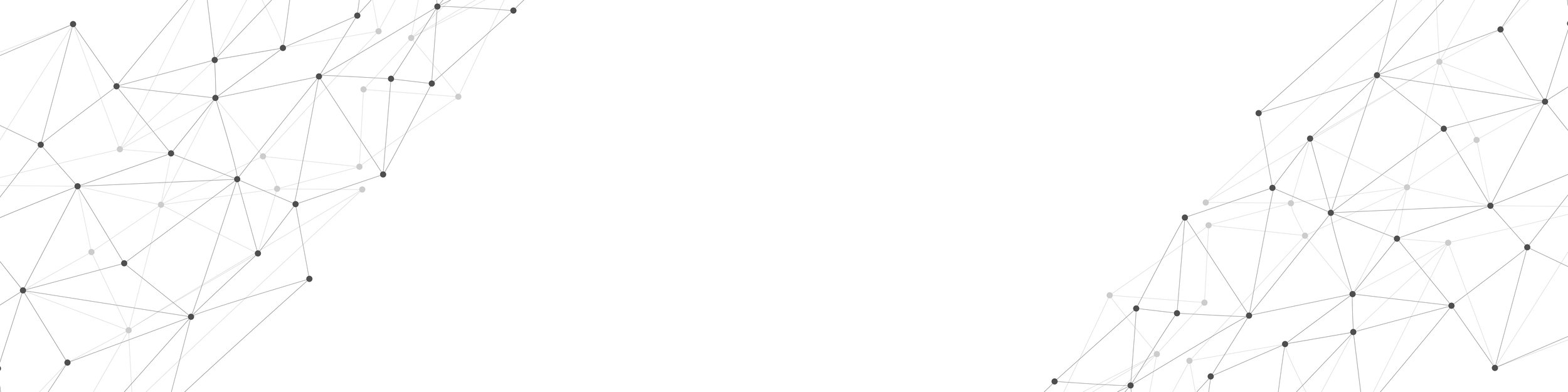
Selective Laser Sintering (SLS)
Manufacturing Partner Certifications - ISO 9001:2015 | AS9100D | ITAR Registered
Helping to Transform Your Ideas into Reality with Lightning Speed
At Mecca, we understand that bringing innovative ideas to life requires speed, precision, and expertise. That’s why we offer top-tier rapid prototyping services to help you turn your concepts into tangible products faster than ever before. Whether you’re a startup looking to launch your first product or an established company seeking to streamline your development process, our rapid prototyping solutions are designed to meet your needs.
What is Selective laser sintering?
Selective laser sintering (SLS) is an industrial 3D printing process that produces accurate prototypes and functional production parts in as fast as 1 day. Multiple nylon-based materials and a thermoplastic polyurethane (TPU) are available, which create highly durable final parts that require heat resistance, chemical resistance, flexibility, or dimensional stability. With SLS 3D printing, no support structures are required making it easy to nest multiple parts into a single build and an economical solution for when higher volumes of 3D-printed parts are required.
Common uses for selective laser sintering are:
jigs and fixtures
housings
snap fits and living hinges
Selective laser sintering (SLS) uses a CO2 laser that fuses nylon-based powder, layer by layer until final thermoplastic parts are built.
*General Material Selection available through our external Manufacturing Suppliers.
-
PA 11 Black (PA 850) provides ductility and flexibility without sacrificing tensile strength and temperature resistance. These characteristics make PA 850 a widely used general-purpose material for functional and moving parts.
Primary Benefits
Highest elongation at break of all additively manufactured nylons
Uniform deep-black color that showcases features and provides a clean appearance
-
PA 12 White (PA 650) is a go-to material for general-purpose applications like functional and end-use parts. PA 650 is the strongest of the unfilled nylon materials and it is slightly stiffer than PA 11 Black.
Primary Benefits
Economical material choice
Strength and stiffness
-
PA12 Mineral-Filled (PA620-MF) is a 25% mineral fiber-filled PA powder. The fiber content significantly increases stiffness and HDT (up to 363 °F). It is a good material option when stiffness and high temperature resistance are important requirements.
Primary Benefits
Highest stiffness of all additively manufactured nylons
Temperature resistance
-
PA12 40% Glass-Filled (PA614-GS) is a PA powder loaded with glass spheres that make it stiff and dimensionally stable. This material is an ideal candidate for parts that require long term wear resistance properties. Due to the glass additive, it has decreased impact and tensile strengths compared to other nylons.
Primary Benefits
Long-term wear resistance
Increased stiffness
-
Polypropylene Natural offers chemical resistance properties that are top among the SLS and MJF material offerings. This tough and durable, yet flexible, material offers resistance to most acids and is a low weight material option.
Primary Benefits
Chemical resistance
Durable, low weight material
-
TPU 70-A is a white thermoplastic polyurethane that combines rubber-like elasticity and elongation with good abrasion and impact resistance properties. The rubber-like quality of this material make it ideal for seals, gaskets, grips, hoses, or any other application where excellent resistance under dynamic loading is required.
Primary Benefits
High elongation at break
Flexibility
Post-Processing Capabilities for Selective Laser Sintering (SLS) Printed Parts
Surface finish on SLS parts is typically rougher than other 3D printing technologies—it can range from 100-250 RMS. We also bead blasts the majority of customers’ parts to remove loose powder and create a smooth matte finish. Vapor smoothing is a post-processing option available for PA11 Black parts, which will result in surface finish roughness between 64 – 100 μin RA.