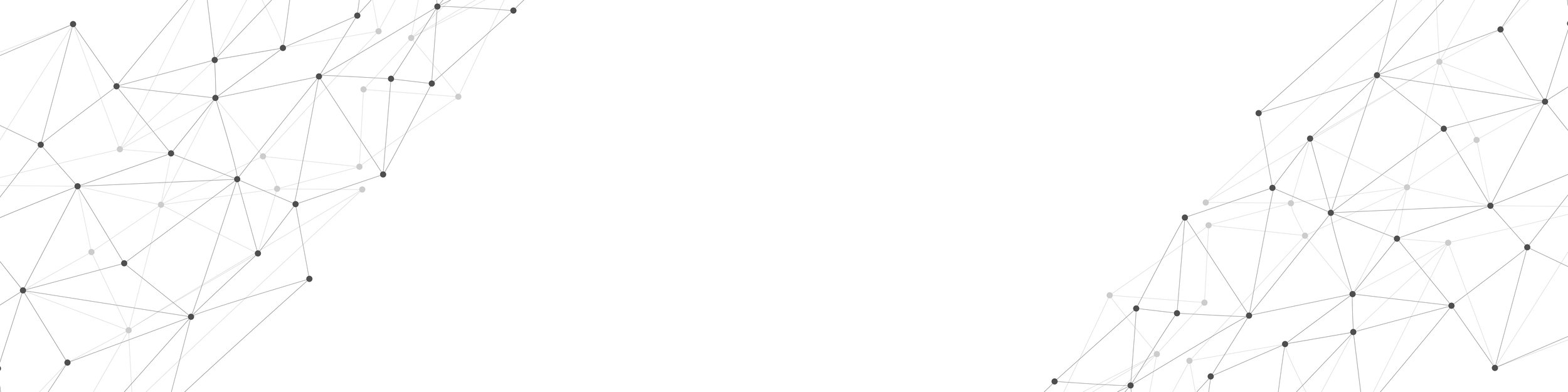
Metal 3D Printing
Manufacturing Partner Certifications - ISO 9001:2015 | AS9100D | ITAR Registered
Helping to Transform Your Ideas into Reality with Lightning Speed
At Mecca, we understand that bringing innovative ideas to life requires speed, precision, and expertise. That’s why we offer top-tier rapid prototyping services to help you turn your concepts into tangible products faster than ever before. Whether you’re a startup looking to launch your first product or an established company seeking to streamline your development process, our rapid prototyping solutions are designed to meet your needs.
What is Direct metal laser sintering?
Direct metal laser sintering (DMLS) is an industrial metal 3D printing process that builds fully functional metal prototypes and production parts in 7 days or less. A range of metals produce final parts that can be used for end-use applications.
Metal 3D printing technology is commonly used for:
Prototyping in production-grade materials
Complex geometries
Functional, end-use parts
Reducing metal components in an assembly
Direct metal laser sintering (DMLS) uses a fiber laser system that draws onto a surface of atomized metal powder, welding the powder into fully dense metal parts.
*General Material Selection available through our external Manufacturing Suppliers.
-
Stainless Steel 17-4 PH is a precipitation hardened stainless steel that is known for its hardness and corrosion resistance. If needing a stainless steel option, select 17-4 PH for its significantly higher tensile strength and yield strength, but recognize that it has far less elongation at break than 316L. Final parts built 17-4 PH receive vacuum solution heat treatment as well as H900 aging.
Primary Benefits
Heat treated for full hardness and strength
Corrosion resistance
-
Stainless steel 316L is a workhorse material used for manufacturing acid and corrosion resistant parts. Select 316L when stainless steel flexibility is needed; 316L is a more malleable material compared to 17-4 PH. Final parts built in 316L receive stress relief application.
Primary Benefits
Acid and corrosion resistance
High ductility
-
Aluminum (AlSi10Mg) is comparable to a 3000 series alloy that is used in casting and die casting processes. It has good strength -to-weight ratio, high temperature and corrosion resistance, and good fatigue, creep and rupture strength. AlSi10Mg also exhibits thermal and electrical conductivity properties. Final parts built in AlSi10Mg receive stress relief application.
Primary Benefits
High stiffness and strength relative to weight
Thermal and electrical conductivity
-
Inconel is a high strength, corrosion resistant nickel chromium superalloy ideal for parts that will experience extreme temperatures and mechanical loading. Final parts built in Inconel 718 receive stress relief application. Solution and aging per AMS 5663 is also available to increase tensile strength and hardness.
Primary Benefits
Oxidation and corrosion resistance
High performance tensile, fatigue, creep, and rupture strength
-
Cobalt Chrome (Co28Cr6Mo) is a superalloy is known for its high strength-to-weight ratio.
Primary Benefits
High performance tensile and creep
Corrosion resistance
-
Titanium (Ti6Al4V) is a workhorse alloy. Versus Ti grade 23 annealed, the mechanical properties of Ti6Al4V are comparable to wrought titanium for tensile strength, elongation, and hardness. Final parts built in Ti6Al4V receive vacuum stress relief application.
Primary Benefits
High stiffness and strength relative to weight
High temperature and corrosion resistance
Post-Processing Capabilities for Metal 3D-Printed Parts
Improve strength, dimensional accuracy, and cosmetic appearance of final metal components with DMLS for production.
Surface Finishing
3- and 5-axis milling
Turning
Polish (Mirror or Brushed)
Passivation
Wire EDM
Tapping and reaming
Mechanical Testing
Tensile
Rockwell Hardness
Heat Treatments
Stress relief
NADCAP heat treatment
Hot isostatic pressing (HIP)
Solution annealing
Aging
Powder Analysis & Material
Traceability
Chemistry
Particle size and distribution analysis